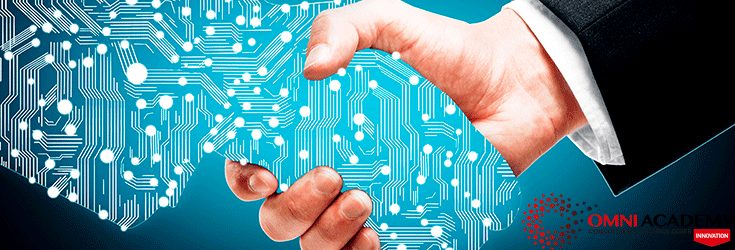
SAP MM Interview Questions & Answers – SAP Materials Management
In this section, we’ll discuss the most important SAP MM Interview Questions. Go through our expert compiled questions and answers to learn about SAP MM, Inventory data, Master data, RTP, RFQ and Invoice processing. Learn SAP MM from Intellipaat SAP MM course and excel in your career.
SAP MM Interview Questions & Answers – SAP Materials Management
1. What is SAP MM and what do you know about it?
It is one of the modules in SAP that deals with the management of materials and procurement process. It also includes master data, account determination, material valuation, inventory management, invoice verification, material requirement planning, etc.
2. List out the essential components of material management.
- Determine requirements
- Source determination
- Vendor Selection
- Order Processing
- Order follow up
- Goods receipts and Inventory management
- Invoice Verification
3. What are the benefits or uses of material management?
- Material valuation
- Multi-location inventory
- Bin management
- The lot and serial traceability
- Product life cycle management
- Inventory replenishment
- Scheduling and resourcing
4. What are the features of material management?
- Purchasing
- Production and material control
- Non-production stores
- Transportation
- Material handling
- Receiving
5. What is material requirement planning (MRP)?
It is a module in SAP enterprise resource planning. It is a type of planning tool to help production and procurement planners to create feasible and realistic plans which helps to quickly initiate procurement and production process.
6. What is consumption-based planning (CBP)?
It is based on past consumption values which makes use of the forecast or other statistical procedures to determine future requirements. It is triggered when the stock level falls below a predefined reorder point or by forecast requirements calculated using past consumption values.
7. What is the difference between MRP and CBP?
In material requirement planning, the prediction of material requirement is based on sales and operations planning while in, consumption-based planning the prediction of material requirement is made, based on historical demand for materials.
8. What is Master production schedule (MSP)?
It is a plan for individual commodities to be produced in each time period such as staffing, production, etc. It is mostly linked with manufacturing in which the plan denotes when and how much of each product will be demanded.
9. What is a planned order in material management?
A planned order is sent to an industry and is a material requirement planning request for the procurement of a particular material at a determined time. It specifies when the internal material movement needs to be made and the amount of material that is demanded.
10. What is production order and purchase order?
A production order determines which material is to be prepared, at which location, and at what time and how much quantity is required. It also defines which components and sequence of operations are to be used and how the order costs are to be resolved.
A purchase order is a formal request or guidance from a purchasing organization to a vendor or a factory to supply or provide a certain quantity of goods or services at or by a certain point in time.
11. What is the process order?
Process Orders (PP-PI-POR) are the central component used for the accurate planning and execution of process manufacturing. A process order represents the production of batches (materials) in a production run or the rendering of services.
12. What is a transaction code in material management?
A transaction code (or t–code) consists of letters, numbers, or both, and is entered in the command field at the top of any SAP GUI screen. Each function in SAP ERP has an SAP transaction code associated with it. You can directly access any function in SAP using t-codes.
13. What are contracts in material management?
A contract is a long-term agreement with a vendor to supply a material or provide a service for a certain period of time. These are specified consequently in release orders issued against the contract when the customer requires them.
14. Define purchase requisition.
A purchase requisition is a primary document which is used as part of the accounting method to launch a merchandise or supply purchase. By processing a purchase order, suitable controls can monitor the legitimacy of purchase, as well as identify the business requirement for the products.
15. How do you create and release purchase requisition in SAP material management?
Purchase requisition creation can be done in T-code ME51N and is a straightforward process:
- Execute ME51N transaction.
- Purchase requisition document type: NB – standard.
- Source determination: ON or OFF.
- Header note.
- Material: material number.
- Quantity and UoM.
- Storage location: in which the material is stored.
- Vendor: automatically determined by using source determination – field number
- Tracking number: covered in previous topics, a desired value can be entered manually
- Valuation price: copied from material master data if maintained there, if not must be entered manually (if this field is not set as optional).
- After entering the desired information in the fields, we can save transaction data.
16. What is a special stock in material management?
Special Stocks are the stocks which belong to a company code. These are not placed in any storage location & no physical inventory is performed.
17. Mention the different types of stocks.
A. Valuated Stock
- Unrestricted Stock
- Quality Inspection Stock
- Blocked Stock
B. Non-Valuated Stock
C. Special Stock
- Subcontracting
- Consignment
- Stock Transport Order
- Third Party Processing
- Returnable Transport Packaging
- Pipeline Handling
18. Define consignment stock.
During the consignment process, when a vendor provides material or goods, the company stores it in their stores. The vendor remains the owner of the material until a customer takes it. The liability arises as soon as the material is removed from the stores.
19. What is meant by master data?
Master Data is basically created centrally and is valid for almost all the applications. It remains constant over time but it is required to update it on a regular basis. For example, the Vendor is a type of master data and he is used for creating purchase orders.
20. What is master data management?
Master data management is a comprehensive method of enabling an enterprise to link all of its critical data to a common point of reference. When properly done, MDM improves data quality, while streamlining data sharing across personnel and departments. In addition, MDM can facilitate computing in multiple system architectures, platforms, and applications.
21. What is inventory management?
Inventory management is used to manage the inventory for the goods. It is based on several key processes. Definition of movement types, reservations, goods issue, and goods receipt.
22. What is movement type and mention a few standard movement types?
Movement types are used as indicators of what is the purpose of the goods movement (e.g. from the storage location to a storage location, receipt from the purchase order, issue for the delivery, receipt from production).
23. Define stock population.
Stock population is the total of all stock management units included in an inventory sampling. These stock management units are uniquely defined through the allocation of the stock management levels to a given inventory sampling. As a result, the stock population is also defined when you allocate stock management levels.
24. What is returnable transport packaging (RTP)?
Returnable transport packaging (RTP) is a multi-trip packaging medium in which goods can be transported more than once between retailers and customers.
25. What are quotations in SAP material management?
Quotations in SAP MM are certain requests for vendors which provides us with some information about their best prices, terms and conditions, schedules of deliveries and other information in order to select the best source for our procurement needs.
26. What is a request for quotation (RFQ) document?
RFQ or Request for Quotation also known as Invitation for Bid is a document which an organization submits to one or more potential suppliers to invite them for the bidding process for a product or service.
27. Mention the RFQ process.
For creating a request for quotation RFQ :
- Enter the transaction code or t-code as ME41 (This will lead you to ‘create RFQ’ screen)
- Enter RFQ type as ‘AN’
- Enter the quotation deadline i.e the last date by which a vendor must submit their quotation.
- Enter Purch organization and purchasing group
- Enter the delivery date and Plant
- Click on Enter
- Next, you’ll see a new screen wherein you need to fill the item codes.
- After entering the item codes, enter the vendor details
You can create more requests with different vendor details.
28. What is a request for proposal (RFP)?
RFP or Request for Proposal is a document which requests a proposal, which is generally made through a bidding process by an agency or a company for the acquisition of some commodity, asset, or service to any potential suppliers to submit business proposals.
29. What is a request for information (RFI)?
A request for information or RFI is a basic business process which collects written information about the capabilities of suppliers. It generally follows a format which can be used for comparative purposes.
30. What is the difference between RFQ, RFP, and RFI?
RFI | RFP | RFQ | |
What is invoice processing? | Gathers vendors information | Creates the best project | Gets the best price for a project |
Status of Solution | Not clearly defined | The overview is understood, yet the details need to be defined | Project and details are clearly identified |
Key deliverables | Provides information about the vendors | Statement of work for a project | Pricing details |
31. What is invoice processing?
Invoice processing is a process a company’s account payable uses to manage supplier invoices. It begins when you accept an invoice and ends when payment has been made and reported in the general ledger.
32. What is movement in goods out (MIGO)?
MIGO or Movement in Goods Out is used for goods movement such as goods issue, goods receipt, plant to plant transfer, storage location to storage location transfer, etc. Basically, MIGO is booked by the logistics department where the goods are actually received.
33. What is movement in receipt out (MIRO)?
MIRO or Movement in Receipt Out deals with invoice verification activities for bills raised from the vendors end. So, basically, MIRO is booked by the finance department.
34. What do you mean by goods receipt and post goods receipt?
Goods receipt is the physical inbound transfer for goods or material into the warehouse. It is the transfer of goods which is used to post goods received from external vendors or from in-plant production. All goods receipts result in an increase in stock in the warehouse.
Post-Goods Receipt is used to post the receipt of goods with reference to the purchase order with which the goods were ordered. If the material is delivered for some purchase order, it is important for all of the departments involved that the goods receipt entry in the system references this purchase order.
Popular ERP Courses -Learn Online Now!
SAP Training – ABAP Technical Consultant
SAP MM – Material Management – SupplyChain
SAP Crystal Reports Development
SAP SuccessFactor – Human Resource Management
Oracle Techno Functional Consultant – Oracle Apps R12
Oracle ERP R12 Supplychain Management
Oracle E-Business Suite R12 Applications DBA
Oracle Fusion Financials Cloud – 1Z0-408
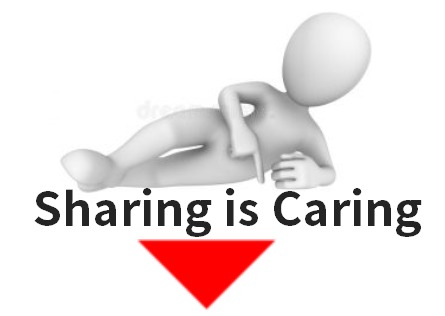